The vast majority of oil-water separators on the market operate according to the "historical" principle of decantation/filtration (Fig.1). In these separators, the condensates enter a large storage tank - the settling tank - or they must stay as long as possible so that the oil rises to the surface and is collected in a storage tank by spillage. The first drawback of the system, this "stagnation" of condensates is conducive to the development of bacteria.

The condensate, pre-separated, is then filtered on 2 elements (polypropylene + activated carbon) then evacuated by overflow to the sewer. This type of system requires precise adjustment of the pouring rings to recover only the oil film on the surface, which is not always very easy. Another drawback is the low separation power on oils with densities close to water (polyglycols in particular).
Their effectiveness is generally imitated at 20 ppm of residual oil in the discharges.
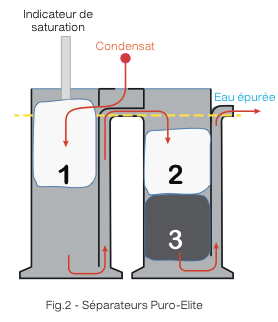
Puro-Elite separators (Fig. 2) work entirely differently. The condensates are not decanted but purified. Here there is only one inlet (raw condensate) and one outlet (purified condensate).
Three filter media (including one floating with a saturation indicator tube) provide extensive filtration of condensate. This technique guarantees the efficiency of 10 ppm maximum in discharges.
For polyglycol type lubricants, specific filter elements allow their separation and guarantee the same efficiency.
Another advantage, and not the least, is that Puro-Elite can process emulsions and accept condensates from any trap technology.
There is no spillway adjustment to be made on these separators, they are ready to operate without previous tedious adjustments.