The Holcim company had huge production problems. In fact, to start on Monday morning in frost, they needed no less than 4 hours to start producing in good conditions. This was due to a poor definition of compressed air production, which is commonly overlooked, consisting of two tank compressors with incorporated refrigeration dryer.
After having defined a complete file for them to remedy these problems, and following the breakage of one of their compressors, we (M.I.B) installed a complete compressed air plant for them consisting of:

- Two COMPAIR compressors at fixed speed (the variable compressor solution being too long to amortize) to compensate for an occasional lack of flow.
- A DELTECH heat-free adsorption dryer, equipped with an energy saver. This option was discussed at length with the client, but thanks to the convincing technical arguments of Max Marsaud, PARTENAIR sector manager, the client did not take long to understand the issue.
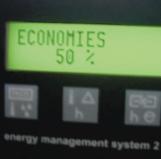
Indeed, with this option, significant energy savings would be achieved. Today with 3000 hours on the dryer counter, the economizer has an energy saving of over 50%. The new configuration made it possible to solve all the startup problems. With this installation, the customer also complies with hydrocarbon discharge standards, thanks to a PURO condensate separator.
Alexis DE WITTE - M.I.B.