Deltech announces the release of its new range of membrane compressed air dryers: D.M.D. series These dryers, using the selective separation technique, cover a range of flow rates up to 190 m3 / h.
The range, made up of 6 models, makes it possible to obtain a pressure dew point between + 3 ° C and -40 ° C. Availability: from December 1st
The advantages of this series are numerous, including: Reduced footprint - No moving parts - No refrigerant or desiccant - No electrical energy required - Low noise level - No maintenance - No additional condensate to treat - A guarantee 3 years.
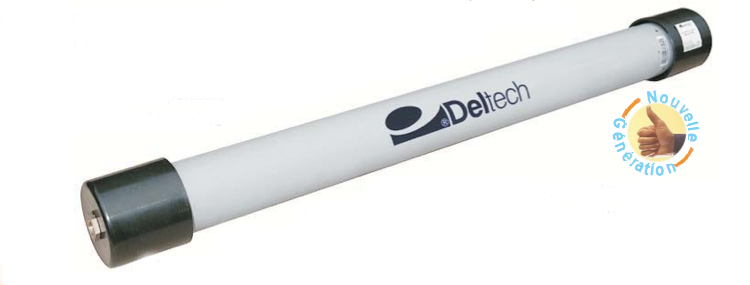
These dryers use state-of-the-art, higher efficiency membranes that use less purge air to obtain the dew point. These membranes provide better performance, greater dry air flow and therefore lower operating costs.
How does a DMD dryer work?
DMD dryers are designed around a patented technology membrane, with an ultra-thin layer, which separates air and water vapor. Hollow fibers, resistant to pressure, are coated with this membrane which lets water pass more than 20,000 times more easily than air. Each dryer is made up of a bundle containing thousands of membranes linked at each end by resin and inserted in a rigid shell.
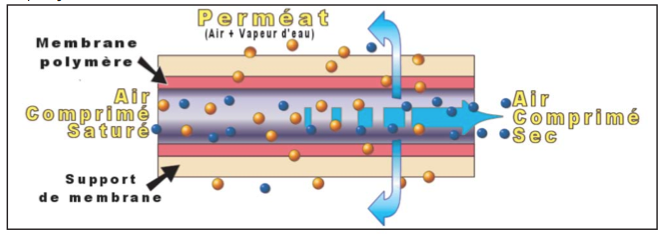
The pre-filtered wet compressed air is sent into the module and circulates inside the hollow fibers. The water vapor contained in the compressed air passes through the membrane and ends up in the shell of the module.
A small part of the dry compressed air leaving the module is injected into the shell, and rejects the water vapor to the outside. This sweeping takes place against the flow of the incoming compressed air.

INSTALLING A DMD DRYER
The diagram below shows the installation of a DMD dryer associated with a dedicated compressor. Extensive pre-filtration is necessary because the membranes must be protected from all the pollutants usually present in compressed air.
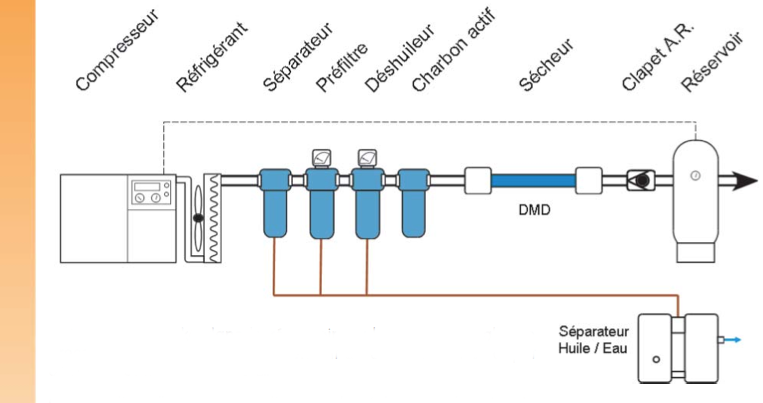
The dry air is stored in the tank on which a pressure switch regulating the operation of the compressor is installed. The non-return valve prevents any loss of air.
This type of installation makes it possible to control the dryer to the needs of the installation, to save the amount of purge air and the energy consumption of the compressor.
On other types of installations (eg bypass on the factory network) it is possible to install a solenoid valve upstream of the dryer, whose operation will be subject to the dry air requirements of the application, which will cut the supply of the dryer with compressed air and thus save sweeping air.
Do not hesitate to contact us for any particular application.
Why advanced filtration?
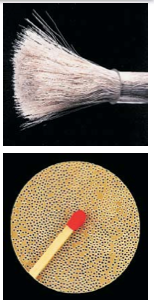
The images on the right speak for themselves!
They represent the bundle and the entry of the bundle of membranes from a dryer.
Here we can see very clearly the small size of the hollow membranes and we understand that any pollution would degrade the performance of the dryer, or even damage it irreparably.
A DMD membrane dryer provides simple, safe and efficient operation, but in return it requires perfectly filtered air (particles, oil, water in liquid phase).