Compressed air is expensive (10 to 20 times more than its equivalent in electrical energy). A properly optimized air production and treatment plant reduce its energy consumption by 20 to 30%. At a time when economies and global warming are mobilizing awareness, here are some “flagship” products that meet user expectations in this area.
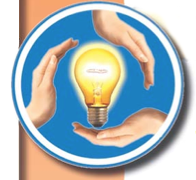
EMS 2: Optimizing dryers
Reducing the energy consumption of adsorption dryers has become the first reflex of any investor.
Adsorption dryers require significant energy to produce dry air. This energy is either fully pneumatic (regeneration without heat) or electric (regeneration by heating resistors). The EMS 2 system considerably reduces the operating cost of DELTECH adsorption dryers by optimizing the energy deployed for the desiccant regeneration as much as possible. His friendly and intuitive interface informs the user of essential information such as the pressure dew point delivered, the savings made, the maintenance required, etc.
It can be installed retroactively on existing DELTECH dryers.
LOCATOR: Tracking Leaks
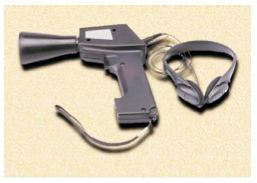
Air leaks in compressed air systems generate phenomenal energy waste. They alone represent (on average) a rate between 20% and 25% of the power of the compressors.
A “small” leak caused by a hole 1 mm in diameter increases the energy bill by around € 300 per year (base € 0.061 per kW). Only significant leaks can be detected by ear. For the others (the most numerous), the LOCATOR is essential. Lightweight, robust, easy to handle, it detects the smallest leaks even on out of reach pipes. An investment with guaranteed immediate profitability ...
EXD: No air lost
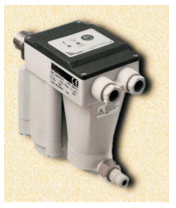
Another item not to neglect: automatic drainers. If their compressed air consumption remains below the 2 stations above, the installation of level detection traps is part of the energy policy for an optimized compressed air plant.
The EXD range of traps, equipped with a microprocessor-controlled control circuit, prevents any loss of compressed air during purge cycles.