In this series of articles we will try to demystify the cold technique used in refrigeration air dryers. Because, if the troubleshooting of air compressors and adsorption dryers does not put technicians off, that of refrigeration dryers almost systematically "kicks them in the towel" to the nearest local refrigeration engineer. However, in the majority of cases, the problem does not require such intervention and can be resolved quickly on site. Our goal is to allow you to diagnose a problem or control the proper functioning of refrigeration dryers on site during routine visits to your customers.
Basic principles...
Paradoxically, to make cold we start by producing. . . heat
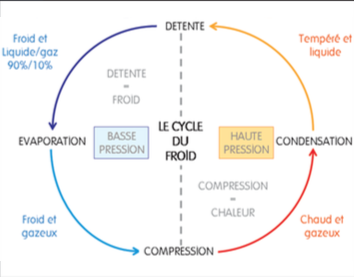
A refrigerant gas compressor (Fréon is a trademark by Dupont de Nemours) compresses the gas (Discharge pressure of around 20 bars and 70 ° C for R 404 A).
It is then necessary to cool and condense this gas, this is the role of the condenser. For the air versions ((by far the most common) a motor-ventilator fixed on a finned condenser extracts the calories towards the ambient air.
At this stage, the refrigerant has lost a good number of calories (+ 10 ° C more than room temperature), but it remains at a high and liquid pressure.
The next step will relax the gas to move it from "warm and liquid" to the "cold and gaseous" state. This action is carried out either by a capillary or by a thermostatic expansion valve. The cold is generated by the expansion of the gas and its evaporation on contact with the warmer parts of the evaporator (also known as the air / Freon exchanger)
After this exchange, the gas (LP and cold) is sucked in by the compressor and the cycle begins again.
Simple controls
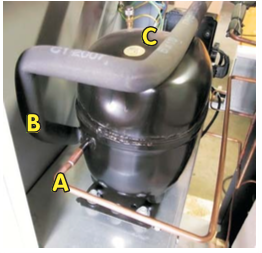
The control of the good functioning of a refrigeration circuit calls upon 2 fundamental concepts, the temperature and the pressure. The temperature can be taken by touch for a first estimate. Besides, you will always see the refrigeration engineers "inspect" the circuit by hand in order to feel the temperature differences at various points well before taking out the pressure gauges and other leak detectors.
Pressure control requires the use of a set of special pressure gauges (B.P. and H.P.). We will come back to this in a future edition.
The first "tip" that we deliver to you today is to take 3 temperatures by hand: delivery, suction and bell of the refrigeration unit. For this, the group must have been in operation for several minutes (It must purr, without excessive noise with a slight vibration) The discharge is the non-thermally insulated copper piping leaving from the compressor. The suction is that of return to the compressor, sheathed in insulating foam, generally black, which must be slightly released in order to feel the temperature well.
The discharge temperature (A) must be hot to very hot. (Take care to avoid any risk of burns), the suction (B) should, on the contrary, be cold). The bell (C) of the compressor must be cool to lukewarm, never hot.
These first impressions make it possible to estimate the proper functioning of the refrigeration compressor as well as the presence of gas in the circuit. There is compression (high discharge temperature) presence of gas and heat exchange (cold return to suction) cooling of the refrigeration compressor with gas (correct bell temperature).